When you need to protect and present your electronics, choosing the right packaging box is key. Custom electronic packaging boxes come in various designs, each serving different purposes. Whether you need durability or style, there is a custom packaging box made to meet your needs.
These boxes offer protection against damage, helping ensure your electronics stay safe during transport or display. Some are designed with added features like cushioning or compartments for multiple items. You can often find options that are easy to personalize with your brand’s colors and logos.
Another important factor is sustainability. Many packaging boxes are made using eco-friendly materials, appealing to those who prioritize the environment. Selecting the right packaging option not only enhances product appeal but also aligns with environmental values.

Overview of Custom Electronic Packaging Boxes
Custom electronic packaging boxes are designed to protect and present electronic products. These boxes come in various sizes and shapes to fit different devices. You can choose from materials like cardboard, plastic, or metal to suit your needs.
One key feature is protection. These boxes safeguard your electronics from damage during shipping and handling. The packaging is often tailored with cushioning to absorb shocks.
Another aspect is branding. With custom packaging, you can add logos, colors, and designs to promote your brand. This helps make your product stand out on the shelf.
Benefits of Custom Packaging:
- Durability: Keeps products safe.
- Brand Visibility: Enhances recognition.
- Cost-Effective: Reduces damage-related costs.
Materials Used:
Material | Features |
---|---|
Cardboard | Lightweight, recyclable |
Plastic | Waterproof, durable |
Metal | Strong, secure |
Custom boxes can also be designed for easy access. You might prefer a box with a simple opening to make it user-friendly.
Customization options are endless. You can select different finishes, colors, and textures. This allows you to create a box that reflects the quality and innovation of your product.
Using custom packaging can enhance the customer experience. It shows attention to detail and can leave a positive impression. Make sure to choose packaging that aligns with both your product and brand goals.

Types of Electronic Packaging Boxes
You have many options when choosing electronic packaging boxes. Different styles include corrugated boxes, rigid boxes, folding cartons, and plastic enclosures. Each type offers unique features that cater to different needs like durability, design flexibility, or cost-efficiency.
Corrugated Boxes
Corrugated boxes are popular for shipping and storage due to their strength. They consist of fluted sheets sandwiched between liners, providing protection against impact. These boxes come in various sizes and thicknesses to fit different products.
Using corrugated boxes ensures safe transportation of electronics, reducing the risk of damage. They are also lightweight, which helps in cutting down shipping costs. Additionally, these boxes are often recyclable, making them a more environmentally friendly option. Customizing prints, sizes, and shapes is easy, allowing for better branding opportunities.
Rigid Boxes
Rigid boxes are known for their robustness and premium feel. Made from high-density cardboard, they provide excellent protection for delicate electronics. These boxes are often used for high-value items, offering an upscale unboxing experience.
You can customize rigid boxes with different finishes like matte, gloss, or lamination. Their durability and quality make them a great choice for gifting electronics or showcasing premium products. Despite being non-collapsible, their sturdy construction makes them reusable, adding to their value.
Folding Cartons
Folding cartons are lightweight and versatile. Made from flexible paperboard, they can be easily folded for storage and transport. These boxes are ideal for product packaging on retail shelves where visual appeal is important.
You can print designs and product information directly on the surface of folding cartons, making them a powerful branding tool. They are cost-effective and suitable for small to medium-sized electronics. While less protective than corrugated options, their convenience and customization potential make them a popular choice.
Plastic Enclosures
Plastic enclosures offer durability and resistance to moisture, chemicals, and impact. These are often used for housing electrical components and products needing extra protection. Various plastics like polyethylene, polypropylene, or polystyrene can be used based on the packaging needs.
You can choose from a range of clear or colored options, allowing product visibility and aesthetic flexibility. Plastic enclosures are often reusable and can be designed in various shapes and sizes. They provide a modern look and are ideal for protecting electronics from environmental factors.
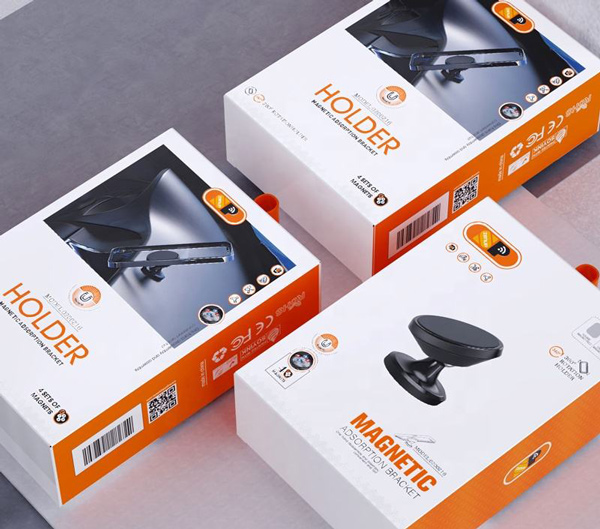
Design Considerations for Electronic Packaging
When designing electronic packaging, you need to focus on aspects like protection, electromagnetic safety, heat control, and movement. These factors ensure the reliability and effectiveness of your products.
Protection and Durability
Protection is crucial for maintaining the function of electronic devices. Consider the materials that will shield against physical damage such as drops, scratches, and bumps. Sturdy materials like metal or high-impact plastics are common choices.
Beyond external impacts, environmental factors such as moisture, dust, and temperature changes can also pose threats. Waterproofing features and sealed enclosures are essential for devices exposed to harsh conditions. By paying attention to these details, you can greatly extend the lifespan and durability of your electronics.
Electromagnetic Compatibility
Electromagnetic compatibility (EMC) is important to prevent interference from other devices. Unwanted electromagnetic emissions can affect performance. Use shielding materials like copper or aluminum to contain emissions.
Compliance with EMC regulations should be a priority. You should conduct testing to ensure your devices do not cause electromagnetic interference. Proper EMC design avoids potential compliance issues and ensures your product operates smoothly in various environments.
Thermal Management
Electronics generate heat that can cause malfunctions. Efficient thermal management is crucial. Integrate systems such as heat sinks, fans, or thermal pads to dissipate heat.
Consider the placement and size of components as they can influence airflow and cooling efficiency. Materials with good thermal conductivity, such as aluminum or copper, are preferred for enclosures. Planning for heat control maintains performance and prevents damage over time.
Portability
Portability affects design, especially for handheld or portable devices. Compact, lightweight materials are ideal. Ergonomic designs make devices easy to carry and use.
Power management is also a vital factor in portable electronic packaging. Consider battery life and charging solutions to meet user needs. Look for a balance between functionality and convenience to create a seamless experience for users. Focus on how easy and efficient your product is to transport and operate.
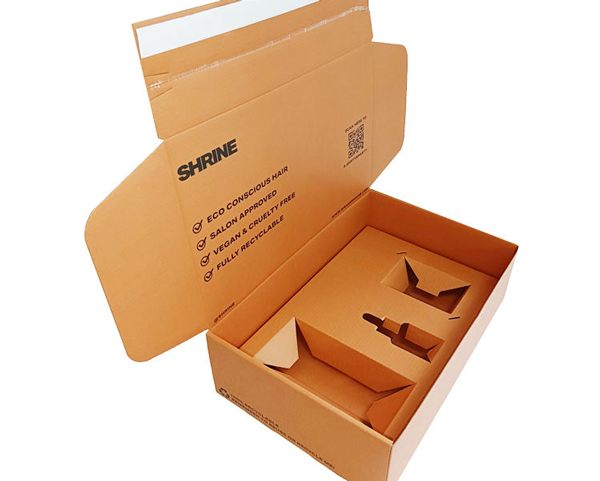
Material Selection for Electronic Boxes
Choosing the right materials for electronic packaging is crucial. It affects durability, protection, and cost. Different materials like cardboard, metal, foam, and plastics have their own benefits and uses.
Cardboard and Paperboard
Cardboard and paperboard are popular choices for electronic packaging. These materials are lightweight and cost-effective. They are commonly used for outer boxes and can be easily customized with printing and branding options. Cardboard offers good protection against dust and other environmental factors.
Paperboard is slightly thinner but provides a smooth surface for high-quality printing. It’s important to consider the strength and thickness needed for your product. Additionally, both materials are recyclable, making them a more sustainable option. Cardboard and paperboard are ideal for products that require simple, protective packaging.
Foam Inserts
Foam inserts play a significant role in protecting electronic components. They serve as cushioning material that can absorb shock and prevent damage. Available in different types like polyurethane, polyethylene, and polystyrene, each has its own level of softness and protection.
You can have foam inserts cut to fit specific shapes, ensuring a snug fit around your electronics. Foam is critical for fragile or sensitive products that need extra care during shipping and handling. It’s lightweight and can be easily customized to match the exact specifications of your product. Foam inserts ensure that delicate items remain securely positioned within the box.
Metals
Metallic materials, such as aluminum and steel, are used for electronic packaging that requires high strength and durability. Metals provide excellent protection against physical impacts and can also offer shielding against electromagnetic interference (EMI). This is especially important for certain electronic devices.
Aluminum is lightweight and resistant to corrosion, making it a preferred choice when weight is a factor. Steel, on the other hand, offers more robust protection and is well-suited for industrial equipment. Metal boxes are typically more expensive but provide long-lasting performance. They are ideal for environments where electronics are exposed to harsh conditions.
Plastics
Plastics are versatile and commonly used in electronic packaging. Polyethylene, polycarbonate, and polypropylene are some examples. Plastics can be molded into various shapes and sizes to fit any design requirement. They are lightweight, durable, and offer good resistance against moisture.
Plastics can also be made transparent, useful for products where visibility is important. The flexibility in design and cost-effectiveness makes them a popular choice for many electronics. Some plastics are recyclable, contributing to environmental sustainability. It is vital to select the right plastic based on the level of protection and flexibility required for your product.

Customization Techniques in Electronic Packaging
Custom electronic packaging boxes come with various customizations to meet specific needs. These techniques enhance function, design, and protection.
Printing and Graphics
Printing transforms plain boxes into branding tools. You can add logos, product details, and appealing images. Digital and offset printing are common methods. With digital printing, fewer colors and details can be printed quickly. Offset printing suits larger quantities with high-quality detail. You might choose embossing or debossing for a tactile and classy look. UV printing adds shiny areas, making logos stand out. With the right graphic design, your brand message becomes clear and attractive, delivering a memorable experience.
Die Cutting
Die cutting shapes your packaging into perfect forms. Custom shapes and openings are easy to create using this method. It uses a steel die to cut through materials with precision. You can have unique designs like windows, handles, or compartments. This helps improve both function and appearance. Exact cuts make assembling boxes efficient and less wasteful. Choosing the right die cut pattern ensures your packaging stands out and is user-friendly.
Lamination and Coatings
Adding lamination and coatings strengthens boxes and enhances their look. Matte or glossy finishes are popular options. Matte lamination gives a smooth, non-reflective feel. Glossy finishes add shine and are eye-catching. Both protect against moisture and scratches. Specialty coatings like soft-touch or anti-scratch offer even more durability and appeal. A box’s tactile feel can greatly influence customer perceptions of a product. Choosing the right finish can add elegance and protection to your packaging.
Foam Fabrication
Foam fabrication provides cushioning and protection for delicate electronics. You can customize foam inserts to fit products perfectly. It reduces damage during shipping and handling. Foam comes in various types, such as polyurethane and polyethylene, each offering different levels of protection and support. Die-cut foam allows for intricate shapes, ensuring alignment and stability. The right foam choice helps maintain product integrity and is essential for sensitive electronic items.
Environmental Considerations
Choosing the right electronic packaging boxes involves thinking about how they affect the environment. You must consider if the boxes are recyclable and what materials they are made of to ensure they are eco-friendly.
Recyclability and Sustainability
Recyclability is crucial when choosing packaging options. Look for boxes made from materials like cardboard or specific plastics that can easily be recycled. Recycling helps reduce waste and conserves natural resources. Check labels that signify recyclability, such as the Mobius loop.
Consider sustainable sources for these materials. Sustainable materials come from renewable sources, like woods from managed forests or recycled components. This reduces the impact on the environment and helps maintain ecological balance. Using recycled materials also reduces the demand for new raw materials.
Biodegradable Materials
Biodegradable materials are essential in reducing landfill waste. These materials break down naturally over time, usually through exposure to microbes. They transform into non-toxic substances such as water, carbon dioxide, and biomass, minimizing environmental impact.
Some options for electronic packaging include materials like bioplastics made from cornstarch or sugarcane. These can degrade faster than traditional plastics. Keep in mind, though, that conditions such as temperature and moisture levels can affect the degradability rate of these materials. Choose biodegradable options to help minimize waste and support a healthier planet.
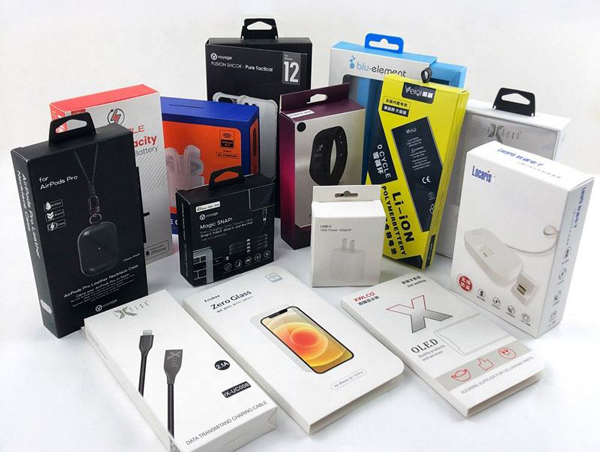
Packaging Prototyping and Testing
Prototyping is a crucial part of designing custom electronic packaging boxes. It helps you see how the finished box will look and perform. You can create physical samples to test different designs easily.
Key Benefits of Prototyping:
- Visual Inspection: Check the look and feel of your custom box design.
- Material Testing: Experiment with different materials to find the best fit.
- Design Validation: Confirm that the design meets all requirements.
After prototyping, testing ensures that your packaging is safe and effective. It helps catch any problems before production.
Important Testing Methods:
- Drop Tests: Make sure boxes can handle drops and impacts.
- Temperature Tests: Test packaging in various temperature conditions.
- Vibration Tests: Ensure boxes stand up to vibrations during shipping.
Testing makes sure your custom packaging boxes are reliable. By using prototypes and testing, you can refine designs and improve quality. This ensures that your product is well-protected and ready for the market.
Case Studies: Innovative Electronic Packaging Solutions
XYZ Electronics made waves by using environmentally friendly materials for their packaging boxes. They created a design with biodegradable plastics and recycled cardboard. This reduces waste and appeals to eco-conscious consumers. Their efforts showcase how sustainable practices can go hand in hand with innovative packaging.
In another case, UnicoPKG developed a sleek, magnetic closure system for their device boxes. This feature not only enhances security but also adds a premium feel. Customers appreciate the ease of opening and closing, providing a satisfying experience that reflects the quality of the product inside.
These examples reflect how electronic packaging can be both creative and practical, meeting various consumer needs while setting new industry standards.